Workflow
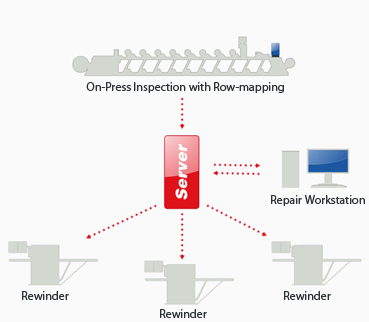
Production in a modern print factory is segmented in three technological steps – prepress, printing and finishing. These are implemented by three distinctive sets of production equipment and most printing companies have these three departments. Quality control has traditionally concentrated on optimizing separately each of these steps.
The term “workflow” relates to the use of information spanning over more than one of these production steps. Information from the inspection system on the printing press about defect type, position and image is stored in a server and then used during the finishing process to selective remove waste stretches of material.

To make this information flow smoothly, the defect data is organized in rolls and each one is marked with a unique barcode, linking it to the correct defect data. When the roll arrives at the rewinder, this information is retrieved and loaded in the control system of the rewinder. It can now rewind to the first mistake, show it on screen and assist the operator in repairing it.
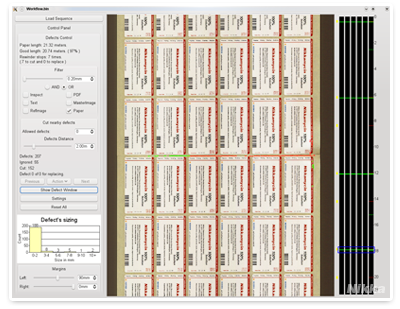
The most significant advantage of workflow technology is the ability to review and edit the defect maps before the ready rolls arrive at the rewinder. Operators at review workstation can filter insignificant defects, aggregate defect groups for repair through splicing and thus find the optimal finishing format for the job. Finishing is streamlined by reducing the number of stops and operating the rewinder at higher speeds.
The downside of workflow is the complicated and voluminous data storage and the need for web marking, required to link to the stored data. Several methods using flags or ink-jetted codes are used to guarantee that positional information is not lost in case of web breaks.
Workflow is optimal for high volume label production with some tolerance toward defects. If the intermediate optimization is done concurrently with printing, risk of reprints can be significantly reduced. Workflow is an inter-process optimization, that can further improve productivity and efficiency.